Boyd SmartCFD: A More Intelligent CFD Software
As market pressures demand higher product performance in smaller form factors power densities have increased exponentially. This has resulted in more complex thermal solutions to the point that current modeling software is no longer capable of accurately predicting product performance.Allows Users to Simulate the Flow Characteristics and Thermal Performance
Boyd, has developed Boyd SmartCFD to bridge the gap between theoretical and real world thermal performance. Boyd SmartCFD has encrypted decades worth of manufacturing expertise, testing, and performance data into Smart Object models for improved thermal design and analysis. With increased accuracy for complex systems, assemblies and components, Boyd SmartCFD enables reduced design cycles, prototype testing, and project costs.
Boyd SmartCFD is a new simulation software that allows users to simulate the flow characteristics and thermal performance inside both simple and complex systems. It is optimized for detailed heat transfer and fluid flow simulations in electronic systems and offers streamlined use through automation tools, intuitive design interface and multiple solver options. These solver options range from an efficient, correlation-based System Solver and a detailed Computational Fluid Dynamics (CFD) Solver. Users like engineers and scientists can benefit from Boyd SmartCFD since it helps increase a product’s quality, reduce its time-to-market, and cut design costs.
Aftermarket Heat Exchanger Core Replacements
Boyd SmartCFD is a total thermal management design tool that can be used to solve component-level, board-level, or system-level applications. It provides design engineers with the ability to test conceptual designs under operating conditions that may be impractical to duplicate with a physical model and obtain information at locations that might otherwise be inaccessible for monitoring.
Boyd SmartCFD is ideal for modeling heat pipes, forced and natural convection systems, liquid cold plates and systems, heat exchangers custom heat sinks, thermal electric coolers and generators (TECs or TEGs), LEDs, electrical traces and fuses, and busbars.
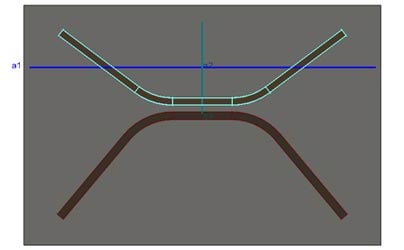
Smart Objects in Boyd SmartCFD
Boyd SmartCFD is the only software tool that accurately models complex two-phase cooling components like heat pipes and vapor chambers, quantifies utilization capacity, and warns of dry-out.
Boyd SmartCFD benefits from decades of empirical data collected by the leading thermal design engineers in the industry. We utilize this data in complex algorithms for accurate and correlated component performance for objects like heat pipes, LED modules, and TECs and TEGs. Users of Boyd SmartCFD can be confident of reported performance since the real world functionality of these advanced assembly components are integrated within the simulation software.
Accelerate Thermal Modeling
Since Boyd SmartCFD is designed by thermal engineers with decades of field experience, the software is streamlined to reduce to complexity common modeling challenges during thermal management solution design. Boyd SmartCFD includes preconfigured geometries for common heat sink constructions, improved tools to characterize liquid flow in heat exchanger and cold plate solutions, and solvers to solve multiple fluid flows for heat exchangers.
Read more about how Boyd SmartCFD accelerates thermal design modeling for these common cooling solutions below:
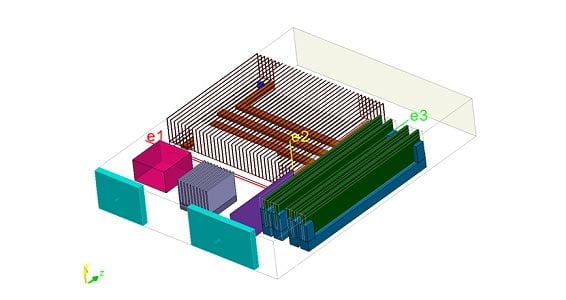
Boyd SmartCFD Solver Options
Boyd SmartCFD is equipped with multiple simulation solvers to address the demands of early to late thermal design cycle needs. Boyd SmartCFD has 3 solvers, each optimized for different applications.
For early conceptual design and quick iterations, Boyd SmartCFD employs a unique System Solver that streamlines calculations by combining correlations and more advanced calculations. The Boyd SmartCFD System Solver uses correlations for heat transfer and friction to realize a 10-20X performance increase over general CFD solvers. With accuracy of -0% + 10% as compared to full CFD results, users can quickly run a multitude of “what-if” scenarios and topologies to narrow in on optimal designs:
Boyd SmartCFD enables customers to use the same model refined with the System Solver with the full Navier-Stokes Computational Fluid Dynamics (CFD) Solver. Full CFD solutions use either a tetrahedral (Tet) or hexahedral (Hex) mesher and is the best solver option when accuracy is of the utmost importance. The full CFD solver is ideal for finalizing thermal management solutions since its high accuracy to real world performance is unparalleled.
Users have the option to combine the speed of the System Solver with the accuracy of the CFD Solver with the use of Boyd SmartCFD’s Hybrid Solver.
The Network Solver can model large liquid systems consisting of a Liquid Cold Plate F-J curve based reduced order models (ROMs) in context with pipes, connectors, manifolds, pumps, and other devices such as valves. By linking in a control monitor the transient response of the system, as a function of changing operating conditions, can be modeled in real time.
Global Parameterization in Boyd SmartCFD
Boyd SmartCFD enables more advanced users to automate and parameterize model construction and environmental conditions. Users can use Global Parameterization to construct complex components like liquid cold plates using parameters for the key dimensions and create new designs instantaneously by just changing a few parameters. This enables users to explore multiple designs faster in the initial development stages of product design. Engineers are able to proceed to prototyping with more confidence in their design by using the Boyd SmartCFD Global Parameterization feature.
The Global Project Parameter Window supports Python syntax where users can define global variables, define custom functions, define lists and dictionaries, and import advanced Python modules for additional functionality. Boyd SmartCFD users can update global variables across multiple components in the model, dynamically adjust relationships between geometries or properties, and automate calculations and model construction for common projects.
The Global Project Parameter Window in Boyd SmartCFD takes thermal simulations to the next level and puts more model construction power into the hands of design engineers and researchers.
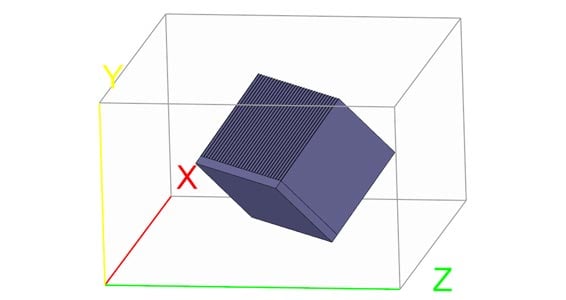
Relative Positioning Systems in Boyd SmartCFD
One of the strengths of Boyd SmartCFD is the Relative Coordinate System functionality. With Boyd SmartCFD’s Relative Coordinate System, components can be arbitrarily rotated within the Solution Domain. This advanced, integrated system enables the position and size of objects to be defined in direct relationship with another component’s properties. This powerful tool streamlines model construction and adjustments between design iterations making thermal design easier and more efficient.
When adding components to a model, they can be positioned relative to the surface of another component. The coordinate system is also dynamic, so that the new component stays “attached” to the parent component and automatically updates when the position or geometry of the parent component changes. Any component’s origin and position or dimensional attributes can be defined as a relation, such as a percentage of a parent component. The Relative Coordinate System enables Boyd SmartCFD to intuitively build accurate and dynamic models quickly, supporting faster design iterations.
The Relative Coordinate System also simplifies parameterized positioning and sizing of individual components in parametric or optimization trials. Since any geometric dimension or coordinate can be defined as a function, advanced applications can utilize the parameterization tools in Boyd SmartCFD to intelligently and automatically define and adjust component dimensions and position.
The Boyd SmartCFD User Interface
Boyd SmartCFD utilizes a typical window-style graphical user interface (GUI) controlled with the mouse and keyboard.
When you open Boyd SmartCFD, the Main Window with several menus will open by default. The GUI consists of several major components: the Main Menu Bar, Toolbars, Project Manager, Property Panel, the Message Window and the 3D Model View. Most actions in Boyd SmartCFD are completed using the Project Manager, the Main Menu, or the Toolbars.
Have questions? We’re ready to help!